Pengelolaan yang efektif dari bahan baku menjadi salah satu kunci kesuksesan dalam dunia produksi. Dalam konteks ini, sebuah metode yang dikenal dengan nama Material Requirement Planning (MRP) dapat diandalkan untuk mengelola kebutuhan material dalam sebuah perusahaan.
Perusahaan manufaktur kadang-kadang melibatkan proses yang cenderung menyimpang dari rencana awal. Namun, potensi peristiwa semacam itu bisa dikurangi atau bahkan dihilangkan sepenuhnya melalui penerapan metode yang satu ini.
Untuk lebih memahaminya, artikel berikut akan mengulas mengenai pengertian MRP, manfaatnya, hingga bagaimana penerapannya pada sektor manufaktur dan distribusi.
Pengertian Material Requirement Planning
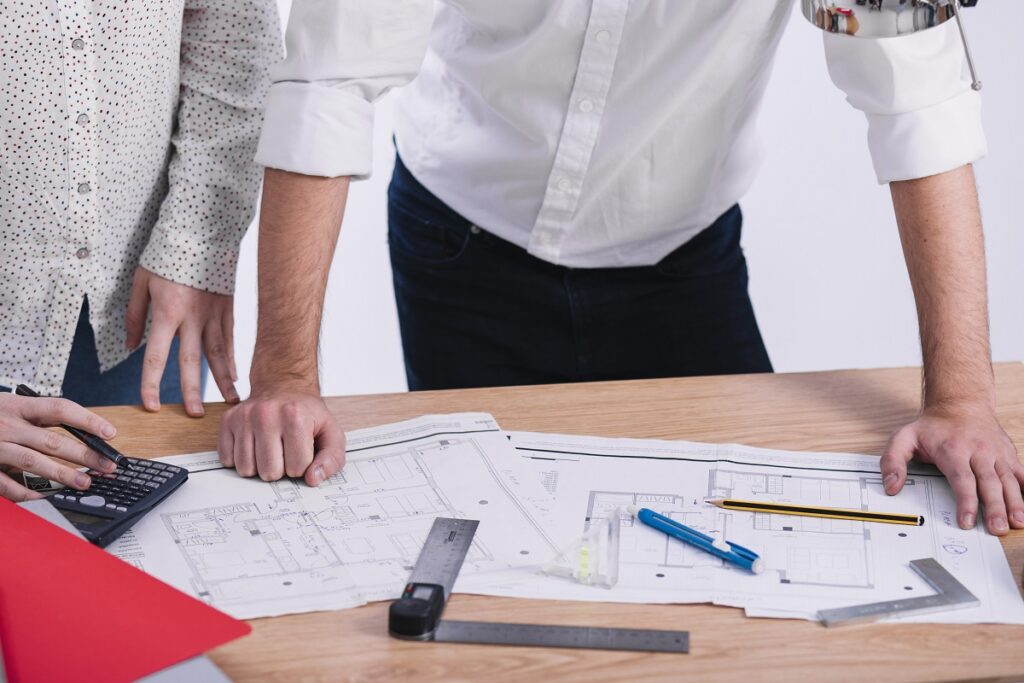
Material Requirement Planning adalah suatu sistem perencanaan yang digunakan untuk mengelola dan mengendalikan inventaris bahan baku dalam sebuah perusahaan. Penerapan sistem ini memungkinkan perusahaan untuk mengetahui informasi terkait jenis, jumlah, dan waktu kapan bahan tertentu diperlukan dalam rangka pelaksanaan proses produksi.
Metode ini mengintegrasikan informasi tentang kebutuhan material, waktu pengiriman, dan jumlah produksi untuk menyusun jadwal yang efisien.
Dengan bantuan teknologi informasi, metode ini dapat memberikan gambaran yang jelas tentang berapa banyak bahan yang diperlukan, kapan dibutuhkan, dan dari mana asalnya.
Ketika diterapkan, perusahaan dapat mengeliminasi risiko terkait kekurangan atau kelebihan persediaan bahan. Sebelum memasuki tahap proses, ada tiga elemen kunci yang diperlukan, yakni rencana produksi utama (master production schedule), daftar bahan (bill of material), dan berkas master inventaris.
Material Requirement Planningsendiri awalnya ditemukan oleh Joseph Orlicky dari J.I Case Company pada sekitar tahun 1960-an. Seiring berjalannya waktu, strategi perencanaan produksi ini telah mengalami empat kali pengembangan untuk menyesuaikan diri dengan kemajuan teknologi dan persyaratan evolusi dalam sistem perusahaan hingga saat ini.
Manfaat Material Requirement Planning

Terdapat sejumlah keuntungan yang dapat dinikmati oleh pemilik perusahaan manufaktur atau produsen yang secara intensif melibatkan diri dalam berbagai proses produksi secara terus-menerus. Dengan menerapkan sistem Material Requirement Planning, beberapa manfaat yang bisa diperoleh di antaranya:
1. Optimasi Inventaris
MRP membantu perusahaan untuk mengoptimalkan inventaris bahan baku. Dengan mengetahui kebutuhan material yang tepat, perusahaan dapat menghindari kelebihan persediaan yang dapat menyebabkan biaya penyimpanan yang tinggi.
2. Peningkatan Efisiensi Produksi
Dengan mengidentifikasi kebutuhan material dengan akurat, memungkinkan perusahaan untuk merencanakan produksi dengan lebih efisien. Hal ini mengurangi waktu yang dibutuhkan untuk menyelesaikan pesanan dan meningkatkan produktivitas.
3. Pengurangan Biaya
Sistem perencanaan ini membantu mengurangi pemborosan dan biaya produksi yang tidak perlu. Dengan mengelola inventaris dengan baik, perusahaan dapat menghindari biaya yang terkait dengan penyimpanan berlebihan dan pemborosan material.
4. Peningkatan Pengelolaan Rantai Pasok
Tidak hanya mengelola kebutuhan material internal perusahaan, tetapi juga membantu dalam koordinasi dengan pemasok. Hal ini memungkinkan perusahaan untuk memastikan ketersediaan bahan baku tepat waktu dan mengurangi risiko keterlambatan produksi.
5. Dapat Menyajikan Solusi Atas Kendala yang Terjadi
Sistem ini dapat mencegah timbulnya permasalahan dalam jalannya proses produksi dan memberikan saran solusi untuk mengatasi masalah tersebut. Hal ini didapatkan dari suguhan analisis data yang bersandar pada data historis sebagai pertimbangan evaluatif guna perbaikan proses pada periode berikutnya.
Penerapan Material Requirement Planning
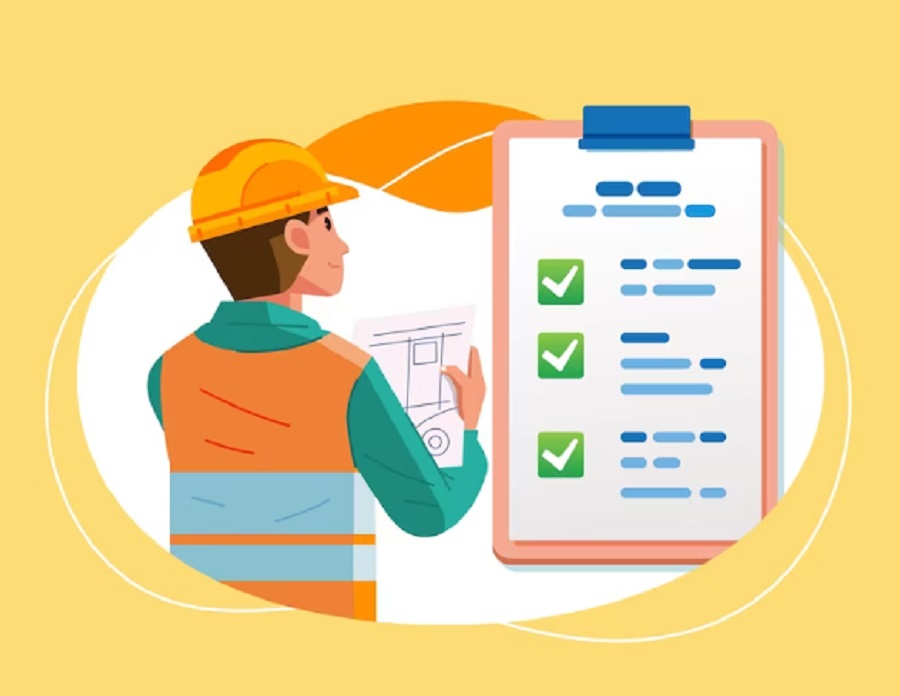
Material Requirement Planning adalah sebuah metode perencanaan dalam suatu sistem produksi yang tentunya memiliki prosedur tersendiri dalam penerapannya. Langkah-langkah dalam prosedur tersebut di antaranya adalah:
1. Identifikasi Kebutuhan Material
Tahapan awal dalam proses ini adalah mengenali keinginan dan kebutuhan pelanggan untuk dapat memenuhinya, dimulai dengan merekam pesanan pelanggan serta melakukan prediksi penjualan (forecasting).
2. Pemeriksaan Inventaris dan Pengalokasian Sumber Daya
Memeriksa stok barang terlebih dahulu dan mengalokasikan sumber daya yang sesuai untuk memastikan pengelolaan yang efektif di dalam gudang atau ruang penyimpanan juga merupakan langkah awal yang krusial. Tindakan ini memberikan transparansi terhadap produk yang dimiliki, lokasi penyimpanannya, dan status prosesnya.
3. Pengembangan Jadwal Produksi
Berdasarkan analisis kebutuhan material, MRP akan menghasilkan jadwal produksi yang rinci. Jadwal ini mencakup informasi tentang waktu produksi, jumlah produksi, dan kebutuhan material harian.
Jadwal produksi juga mengenali peralatan dan tempat kerja yang dibutuhkan pada setiap tahap, serta menghasilkan perintah kerja dan pesanan.
4. Pemantauan dan Pembaruan
Penerapan MRP tidak berhenti pada tahap perencanaan awal. Perusahaan perlu secara teratur memantau dan memperbarui data inventaris dan produksi untuk memastikan perencanaan tetap akurat dan efektif.
Untuk memperjelas pemahaman mengenai langkah-langkah operasional sistem ini dalam berbagai sektor industri, berikut disajikan contoh penerapan Material Requirement Planning pada aktivitas operasional perusahaan di sektor manufaktur:
Sebuah perusahaan manufaktur yang fokus pada produksi komputer dan laptop sedang mengelola beragam bahan baku dan komponen seperti casing, motherboard, prosesor, RAM, hard disk, layar, baterai, dan berbagai unsur lainnya.
Dalam upaya untuk meningkatkan efisiensi persediaan serta proses produksi, perusahaan dapat mengadopsi sistem MRP melalui langkah-langkah seperti berikut:
- Mengenali BOM untuk setiap jenis laptop yang diproduksi.
- Merencanakan produksi berdasarkan permintaan dan analisis pasar dan sistem ini akan memandu jumlah laptop yang perlu diproduksi.
- Menghitung kebutuhan material dengan BOM dan rencana produksi. Contohnya, memproduksi 1000 unit laptop, sistem akan menentukan jumlah casing, motherboard, RAM, prosesor, dan komponen lain.
- Mengevaluasi persediaan untuk memulai produksi. Jika ada kekurangan, sistem akan mengidentifikasi barang yang perlu dipesan atau dibeli.
- Sistem akan menentukan jadwal produksi berdasarkan kebutuhan material dan kapasitas produksi.
- Selama produksi, MRP akan terus memonitor status persediaan dan produksi, serta membantu perusahaan mengambil tindakan korektif dalam menghadapi perubahan permintaan atau masalah rantai pasok.
Adapun contoh penerapannya dalam sektor distribusi adalah sebagai berikut :
Ada sebuah perusahaan distributor yang spesialis dalam mendistribusikan produk elektronik. Perusahaan ini memiliki sejumlah toko ritel yang tersebar di berbagai lokasi dan melayani pesanan dari pelanggan grosir serta e-commerce.
Untuk memastikan ketersediaan produk, menghindari kekurangan persediaan, dan memaksimalkan efisiensi proses distribusi, prosedur MRP yang bisa diterapkan adalah:
- Perusahaan mengumpulkan data historis tentang permintaan produk dari pelanggan ritel, grosir, dan e-commerce, mencakup tingkat penjualan dan tren permintaan masa depan.
- Dengan memanfaatkan data tersebut, perusahaan menggunakan metode forecasting untuk memprediksi permintaan produk dalam periode tertentu.
- Tingkat persediaan optimal dihitung untuk setiap produk, melibatkan pusat distribusi dan toko ritel.
- Sistem akan menghitung kebutuhan material, termasuk pesanan dari pabrikan, alokasi ke toko ritel, dan persiapan untuk pesanan grosir atau e-commerce.
- Persediaan efisien juga akan dikelola untuk memastikan kecukupan persediaan sesuai perhitungan.
- Sistem juga turut menentukan jadwal pengiriman dan distribusi ke toko-toko ritel serta pelanggan grosir atau e-commerce.
- Selama distribusi, sistem ini akan memantau status persediaan dan distribusi, siap mengambil tindakan korektif jika ada perubahan dalam permintaan atau masalah rantai pasokan.
Material Requirement Planning (MRP) adalah alat yang sangat penting dalam mengelola kebutuhan material dalam proses produksi. Dengan memanfaatkan teknologi informasi, sistem perencanaan ini akan membantu perusahaan untuk merencanakan produksi dengan lebih efisien, mengoptimalkan inventaris, dan mengurangi biaya produksi.
Leave a Reply